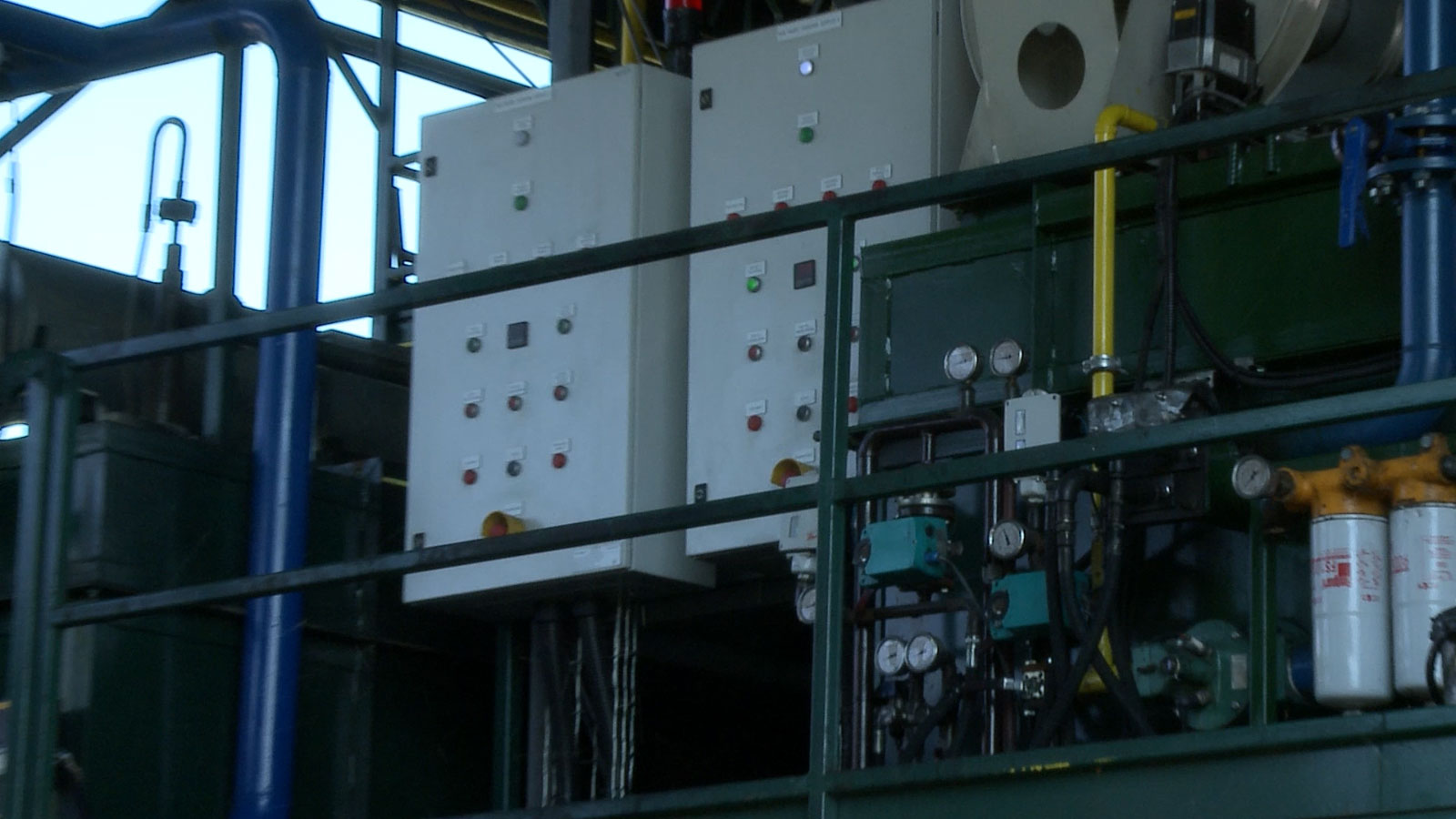
THROUGH OUR COLLECTING NETWORK TIRE WASTE ARRIVES TO OUR SITE. AFTER WEIGHING AND DOCUMENTATION TIRE WASTE IS UNLOADED. AT THE ARRIVAL PLACE OUR LOADERS ARRANGE THE WASTE TO PROCESS, THEY SELECT AND STORE THEM ACCORDING TO THEIR TYPES.
ACORDING TO THE WASTE PROCESSING SCHEDULE, TIRE WASTE GOES TO THE PREPARATORY, GRINDER PLANT (OUR COPORATE GOVERNANCE SHOWS WHICH PRODUCT HAS TO BE PRODUCED FROM WHICH RAW MATERIAL DEPENDING ON THE ORDERS AND STOCK). FIRST OF ALL THE GRINDER CUTS THE TIRES INTO SMALLER PIECES, THEN THESE PIECES GO TO THE SECOND GRINDER. THIS MACHINE CAN SEPARATE THE STEEL WIRES FROM RUBBER AND TEXTILE COMPONENTS, THE SEPARATED STEEL IS STORED IN THE STEEL DEPOT UNTIL TRANSPORTATION. THE SHREDDED RUBBER+TEXTILE FRACTIONS ARE TAKEN TO THE SUITABLE STORAGE WHERE THEY ARE STAYING DRY UNTIL FURTHER PROCESSING.
FURTHER PROCESS CAN PROCEED IN TWO DIRECTIONS:
- WE KEEP GINDING AND MAKE A GRANULATE WHICH CAN BE SOLD TO RUBBER SHEET PRODUCERS
- IT WILL BE A RAW MATERIAL FOR THE PYROLYSIS PLANT AND BE PROCESSED IN OUR REACTORS
WE KEEP REFINING THE GRIST AND MAKE A GRANULATE. THE FINAL GRANULATE IS STORED IN BIGBAGS UNTIL IT’S SOLD. WE SELL THE REMOVED TEXTILE TO CEMENT FACTORIES. STEEL IS SOLD TO STEELWORKS THROUGH MERCHANTS.
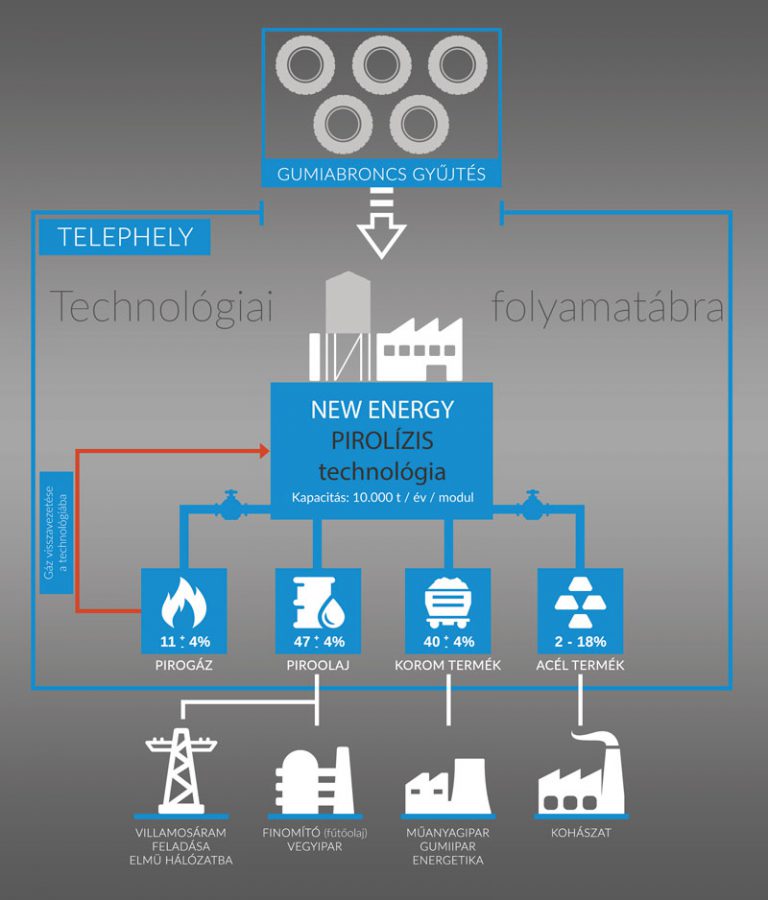
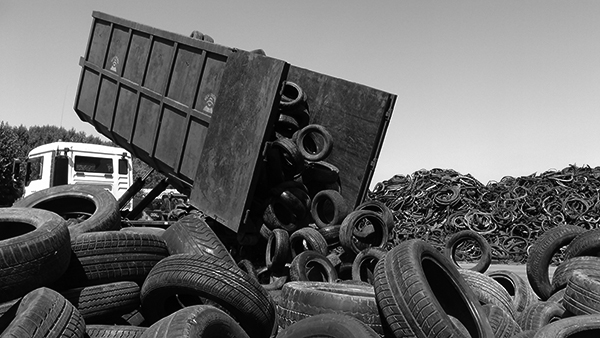
ABOUT PYROLYSIS PLANT:
OUR TECHNOLOGY CONSTANTLY HAS BEEN DEVELOPED FOR 10 YEARS. OUR PLANT OPERATES WITH 2 REACTORS, PROCESSING CAPACITY IS 8.000 TON RUBBER+TEXTILE WASTE/YEAR WHICH MEANS 10.000 TON TIRE WASTE/YEAR CAPACITY.
FIRST OF ALL THE PREPARED RAW MATERIAL GOES TO THE DOSING HOPPER. THIS HOPPER SPLITS THE RAW MATERIAL BETWEEN THE 2 REACTORS. FROM THE HOPPER, RUBBER WASTE GOES TO THE EXTERNALLY HEATED CLOSED REACTOR THROUGH THE SHUTTLE SYSTEM. THE REACTORS ARE SELF DEVELOPED PRODUCTS, PRESENTLY THEY ARE REPLACED TO THE 4TH GENERATION. OUR TECHNOLOGY IS REGISTERED AND PROTECTED BY WORLDPATENT, IT’S OUR PROPERTY. THE SYSTEM IS CONTROLLED BY OUR OPERATORS WITH PLC.
THE REACTOR IS CONTRAST TO THE PRESENTLY AVAILABLE COMPETITIVE PRODUCTS ON THE MARKET, IT’S IN A STANDING POSITION, VERTICALLY
ALIGNED WITH A MIXER IN ITS INNER-CENTRAL PART WHICH CONSTANTLY MIXES THE RUBBER CHIPS. INSIDE THE REACTOR THE TEMPERATURE IS ABOUT 450 C DEGREES CELSIUS DURING OPERATION. WE DON’T USE CATALYST OR ANY BOOSTER MATERIALS.
DURING THE PYROLYSIS PROCESS THE RUBBER POLYMERS BREAK DOWN INTO SMALLER MOLECULES. THESE MOLECULES EVENTUALLY VAPORIZE. THESE VAPORS ARE CONDUCTED IN PIPELINES FROM THE REACTOR TO A HEAT EXCHANGER TO SEPARATE LIQUID AND GAS FRACTIONS. LIQUIDS ARE FURTHERMORE SEPARATED INTO HEAVY AND LIGHT PARTS. AFTER PHYSICAL/CHEMICAL TREATMENTS WE STORE THEM PROPERLY.
RESULTING MATERIALS LEAVING FROM THE SYSTEM DURING THE PROCESS:
- GAS FRACTION (GOES THROUGH DESUPHURIZATION BY LIME-WASH, CONDENSABLE PARTS ARE SEPARATED)
- GASOLINE FRACTION (SEPARATED FROM OIL BY FLASH POINT IN ORDER TO SECURE THE SAFE UTILIZATION OF OIL )
- OIL FRACTION (ONE OF OUR MAIN PRODUCTS, CAN BE USED DIFFERENT WAYS.(REFINERY, POWER PLANT, INDUSTRIAL HEATING OIL, ENERGY PRODUCTION) WATER
IN THE REACTOR, AFTER THE PYROLYSIS PROCESS FINISHES (GAS/VAPOR MATERIALS ARE GONE) STILL REMAINS A SOFT POWDER MATERIAL, THIS IS PYROLYSIS CARBON BLACK. THIS CARBON BLACK IS RELEASED TO A SEPARATING SYSTEM WHERE THE REMAINED POLLUTING SUBSTANCES ARE SEPARATED (KEVLER/ STEEL). THESE MATERIALS ARE COOLED BEFORE PUTTING THEM INTO BAGS FOR CEMENT FACTORY SALES.
DURING SEPARATION CARBON BLACK IS ACTIVATED BY STEAMING. ACTIVE SURFACES OPEN, SO CARBON BLACK FRACTION WILL HAVE A HIGHER ACTIVE SURFACE WHICH IS MORE VALUABLE FOR RUBBER AND PLASTIC INDUSTRY AS RAW MATERIAL. THE READY CARBON BLACK IS STORED IN BIGBAGS OR TAKEN TO SILOS UNTIL IT’S SOLD.
IT’S IMPORTANT TO TALK ABOUT THE HEATING OF OUR REACTOR. WE DON’T USE FOSSIL FUELS (WE DON’T EVEN HAVE GAS ON OUR SITE), THE CLEANED GAS FRACTION RESULTING FROM THE PROCESS IS LEAD TO A GAS TANK WITH A SUPERCHAGER. THIS GAS HEATS THE REACTOR WITH A CLOSED FIREBOX WHICH IS PLACED SEPARATED FROM THE REACTOR IN FRONT.
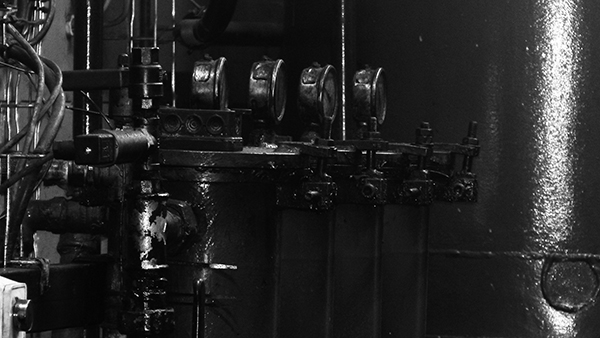
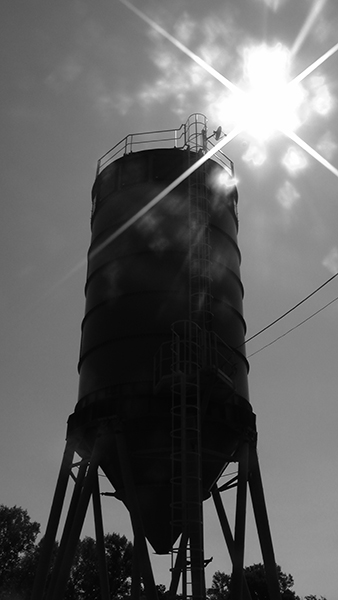
GAS BURNS IN THE FIREBOX. THE FIREBOX IS MADE IN A WAY THAT THERE IS EXTREMELY HIGH TEMPERATURE INSIDE (950-1050 C DEGREES CELSIUS). THE REASON OF THIS IS THAT IN THIS STAGE WE BATCH THE ADDITIVES FOR REDUCING EMISSIONS, THESE TAKE EFFECT ON HIGH TEMPERATURE AND ALSO STACK GAS RETENTION TIME MATERIALIZES (3MP). MEANWHILE THE POSSIBLY RESULTING DIOXINS REACT, THE CARBON MONOXID IS VERY LOW BECAUSE OF THE HIGH TEPMERATURE, WE PUT IN ADDITIVES FOR TREATING NOX AND SOX STACK GAS COMPONENTS. PRACTICALLY, THE HEATING OF OUR REACTOR IS GIVEN BY THE CLEANED STACK GAS FROM WHICH THE POLLUTANTS ARE REMOVED IN ADVANCE. THIS CLEANED , EXTREMELY HOT STACK GAS IS LED TO THE DOUBLE WALLED REACTOR BETWEEN THE 2 WALLS. BETWEEN THESE 2 WALLS GAS GIVES THE HEAT, THE PYROLYSIS GOES ON BEHIND THE INNER WALL, THE OUTSIDE WALL SERVES AS INSULATION.
IT’S IMPORTANT TO NOTE THAT DURING PYROLYSIS WE KEEP CO2 ATMOSPHERE IN THE REACTORS AS WELL AS IN THE CONNECTING SYSTEMS, SO THERE CAN’T BE BURNING IN THE REACTOR. THIS IS THE SUBSTANCE OF PYROLYSIS: RUBBER POLYMERS BREAK DOWN IN A CLOSED SYSTEM WITHOUT OXIGEN HEATED FROM OUTSIDE.
THE END PRODUCTS REMAIN STORED AS VALUABLE SECONDARY RAW MATERIALS UNTIL TRANSPORTATION.